Transform Your Garage: Comprehensive Guide to Estimate of Cost to Epoxy Garage Floor
Ready to take your garage from a cluttered storage space to a sleek, functional area worthy of your home? The secret lies in the floor—epoxy flooring, to be precise. This guide will provide you with a deep dive into the cost to epoxy garage floor with a durable and stylish epoxy coating. We’ll explore factors that influence the price, from square footage and material quality to labor costs. Whether you’re a seasoned DIYer or considering professional installation, our comprehensive insights will ensure you make an informed decision. So, let’s roll up our sleeves and pave the way to a garage that not only looks impressive but also adds value to your home.
Evaluating Your Space: Pre-Installation Considerations
Before diving into the world of epoxy, it’s crucial to assess the current condition of your garage floor. Epoxy adhesion depends on a clean, porous, and defect-free surface to bond properly. Check for cracks, moisture issues, and uneven areas that might need repairs. It’s also important to consider the usage of your space; a high-traffic garage will necessitate a thicker application of epoxy for longevity. Remember that preparation work, such as fixing imperfections and thorough cleaning, can influence the overall cost and success of your epoxy flooring project.
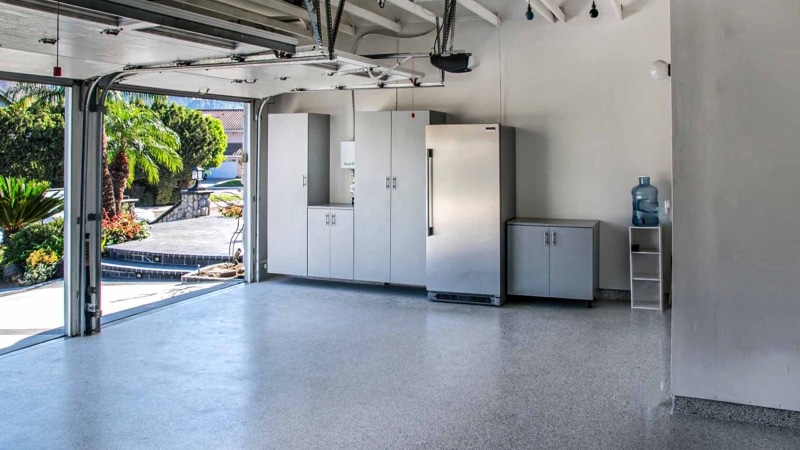
Material Matters: Types of Epoxy and Cost Implications
The type of epoxy you choose is pivotal to both the appearance and functionality of your garage floor. There are primarily two types of epoxy — solid and water-based. Solid epoxy is renowned for its durability and thickness, making it an ideal choice for garages subjected to heavy use. It’s typically costlier than water-based epoxy, which is thinner and easier to apply but may require more frequent touch-ups. Additionally, you may encounter multi-coat systems comprising a primer, color base coat, and topcoat, which offer extended protection but also come with higher material costs. Special additives, like color flakes and slip-resistant coatings, can further customize your flooring but will affect the final price. By selecting the right type of epoxy and considering its long-term maintenance, you can balance your budget with the desired outcome of your flooring project.
DIY Versus Professional Installation
When it comes to applying epoxy flooring, the debate often boils down to two options: tackling the project DIY-style or hiring professionals. Embarking on a DIY project can be a cost-effective solution for those who have the time and confidence in their ability to execute the job precisely. It allows for complete control over the process and can also provide a sense of accomplishment. However, it’s essential to consider the learning curve, as well as the potential for costly mistakes. On the other hand, professional installation offers the advantage of expertise and often comes with guarantees or warranties for the work performed. The trade-off is typically a higher initial investment, but this can often result in superior quality and longevity of the flooring—a crucial consideration when pondering the overall value. Deciding between DIY and professional installation requires weighing the pros and cons against your budget, skill set, and long-term satisfaction with the result.
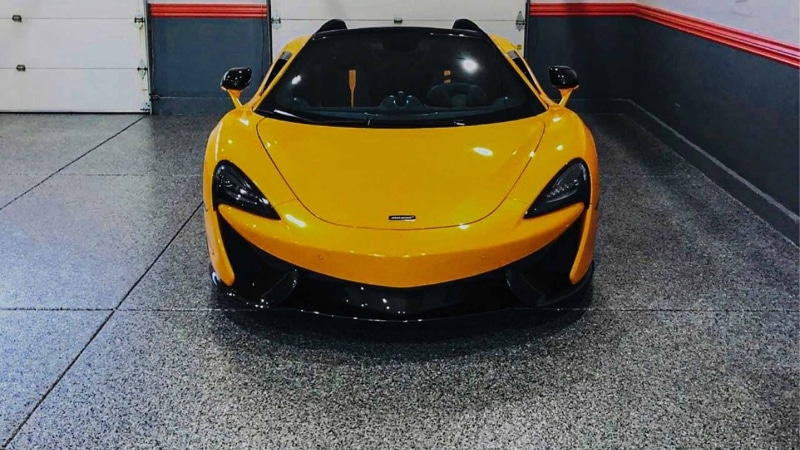
Labor Costs: What Goes into the Pricing?
Professional installation of epoxy garage flooring includes several layers of costs associated with labor. The process starts with the preparation of the surface, which involves repairing cracks, grinding the concrete for proper epoxy adhesion, and cleaning the area meticulously to remove any contaminants. The complexity and time required for this prep work can significantly impact labor costs. The application itself involves multiple steps: priming, applying the base coat(s), broadcasting chips or flakes if desired, and finishing with a top coat that needs to cure properly. The professionals’ expertise, efficiency, and the time it takes to apply each layer accurately are factored into the pricing. Additionally, regional labor rates and the size of the crew required to complete the job on schedule contribute to the total cost. It’s important to bear in mind that choosing a reputable contractor often means higher labor costs, but it also brings the peace of mind that the installation will be performed to high standards, reducing the likelihood of future problems that could lead to additional expenses.
Additional Expenses to Consider
While the primary costs of epoxy flooring center around materials and labor, there are several other expenses that homeowners should account for when budgeting for their garage transformation. These can include the costs of moving and storing belongings during the installation process, as well as the potential rental of machinery or purchase of special tools required for a DIY endeavor. Environmental factors might necessitate a more resilient epoxy formula or additional layers, which can further increase expenses. Moreover, if your garage serves as a workshop or a home for pets, consider the cost implications of alternative accommodations during the curing period. Lastly, for an enduring and polished look, you may want to factor in the long-term cost of maintenance products, such as cleaners and wax designed specifically for epoxy flooring. Planning for these ancillary expenses upfront can help ensure a smooth project flow without unwelcome financial surprises.
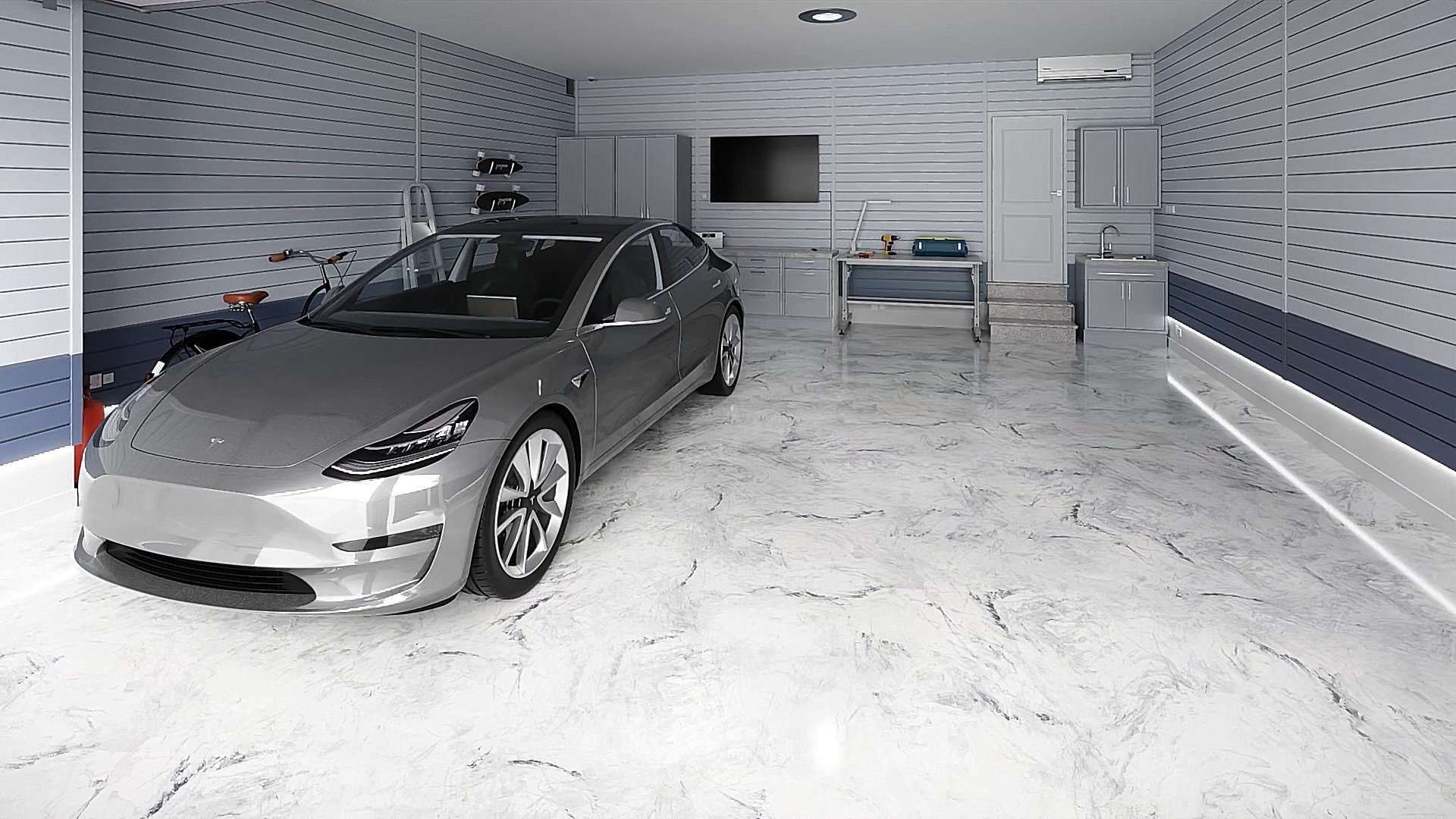
Maintenance and Longevity: Calculating the Long-term Value
After the installation of your epoxy floor, maintenance is key to preserving its aesthetic appeal and structural integrity, contributing significantly to its long-term value. Epoxy flooring typically requires minimal upkeep, such as regular cleaning with mild detergents and avoiding harsh chemicals to prevent surface degradation. It’s crucial to promptly repair any chips or cracks to maintain the protective layer above the concrete. The longevity of epoxy flooring can vary based on the type chosen and the level of traffic it endures, but with proper care, it can last for many years, often outliving other flooring solutions. By adhering to the manufacturer’s maintenance recommendations and performing periodic assessments, homeowners can maximize the investment in their garage’s functionality and appearance. The durability and low maintenance requirements of epoxy ultimately make it a cost-effective choice, offering long-term value and a reduction in the need for frequent renovations.
In conclusion, when considering the investment in epoxy garage flooring, it’s vital to balance upfront costs with long-term gains. The decision to opt for a water-based, solid, or multi-coat epoxy should align with both your current budget and future expectations for the floor’s endurance. Whether you choose the DIY route or professional installation, each choice comes with its own set of cost implications and potential advantages. Remember to account for additional expenses that extend beyond the surface application, and prioritize maintenance to protect your investment. Ultimately, a well-executed epoxy floor offers a functional, durable, and aesthetically pleasing surface that enhances the value of your property for years to come. With careful planning and consideration of the various factors discussed, you can ensure that your investment in epoxy flooring is both satisfying and economically sound.
https://www.google.com/maps?cid=2589512530409833629